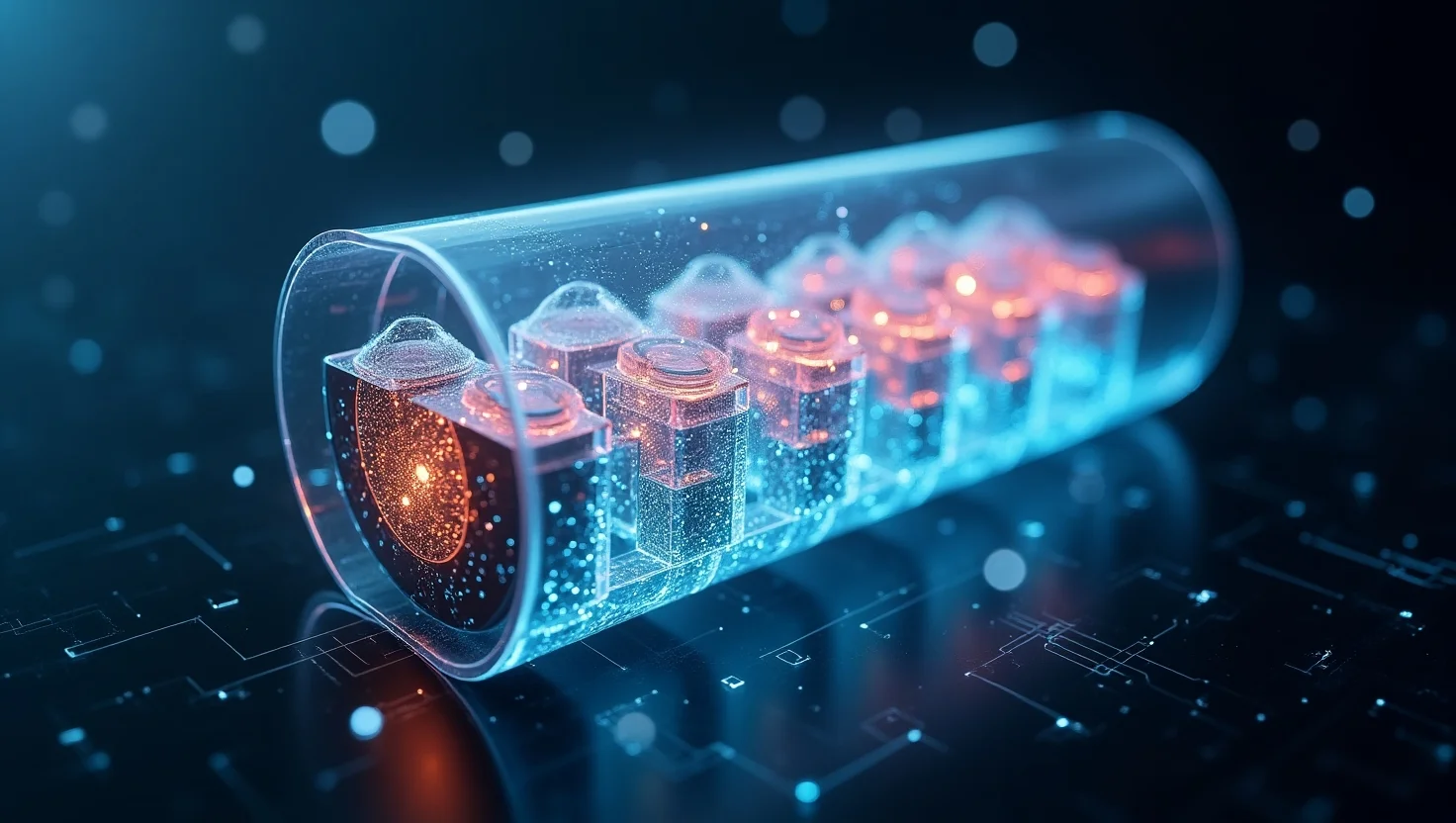
Advancements and Challenges in Solid-State Electrolyte Batteries
5/4/2025
The field of solid-state batteries (SSBs) has witnessed remarkable progress in recent years, driven by innovations in electrolyte materials, interfacial engineering, and manufacturing processes. This study synthesizes cutting-edge research from academic institutions, patent landscapes, and startup innovations, while addressing persistent challenges and proposing solutions. Key developments include breakthroughs in inorganic solid electrolytes achieving ionic conductivities rivalling liquid electrolytes, patent portfolios exceeding 5,800 filings focused on sulfide and oxide-based systems, and startup innovations demonstrating 500 Wh/kg energy densities with 10-minute fast charging capabilities. While technical hurdles remain regarding interfacial stability and scalable production, collaborative efforts between academia and industry suggest commercial viability for electric vehicle applications could emerge by 2030.
Key players include both specialized battery innovators (like QuantumScape, Solid Power, and Factorial Energy) and original equipment manufacturers (OEMs like Toyota, Honda, and Volkswagen) investing significantly to improve performance and safety of the batteries.
Market Opportunities (Key growth Drivers)
Key Technical Challenges (Technical bottlenecks)
Advanced Electrolyte Material Developments:
Interfacial Engineering Breakthroughs:
Manufacturing Process Innovations:
Performance Milestones:
As we stand at the threshold of this battery revolution, the question is no longer if solid-state batteries will transform the energy landscape, but when. Those who solve the core technical challenges while building scalable manufacturing processes will not just disrupt the energy storage market – they'll reshape the future of electric mobility.
Key players include both specialized battery innovators (like QuantumScape, Solid Power, and Factorial Energy) and original equipment manufacturers (OEMs like Toyota, Honda, and Volkswagen) investing significantly to improve performance and safety of the batteries.
Market Opportunities (Key growth Drivers)
Performance Improvements | Safety Benefits | Long-term Cost Advantage |
---|---|---|
Theoretical energy densities up to 1000 Wh/kg | Elimination of flammable liquid electrolytes | Longer lifecycle reduces total cost of ownership |
Faster charging capabilities (potential for 10-minute charging) | Operates safely at higher temperatures | Potential for 20-30% lower pack costs once scaled |
Better low-temperature performance | Reduced need for complex cooling systems | Higher energy density means fewer cells needed per pack |
Extended cycle life (>1000 cycles) | Better abuse tolerance (mechanical, thermal, electrical) | Simplified thermal management systems reduce overall costs |
Key Technical Challenges (Technical bottlenecks)
Material Limitations | Manufacturing Complexity | Interface Engineering |
---|---|---|
High-purity materials increase production costs | Precise temperature control needed during sintering and assembly | Poor contact between solid electrolyte and electrodes creates resistance issues |
Limited suppliers for specialized solid electrolyte materials | Uniformity issues in large-format cells affect performance | Formation of dendrites at interfaces |
Sulfide-based electrolytes are moisture-sensitive, requiring dry room processing | New equipment and processes required | Chemical instability leads to degradation over repeated cycling |
Ceramic electrolytes are brittle and prone to cracking | Achieving void-free interfaces at scale | scaling difficulties |
Advanced Electrolyte Material Developments:
- New classes of sulfide-based superionic conductors like Li10GeP2S12 (LGPS) and argyrodite Li6PS5Cl showing unprecedented ionic conductivities above 10⁻² S/cm at room temperature
- Oxide-based systems like LLZO (Li7La3Zr2O12) garnering attention for their environmental stability and mechanical strength, despite lower conductivities
Interfacial Engineering Breakthroughs:
- Development of artificial solid-electrolyte interphase (SEI) layers using atomic layer deposition (ALD) to mitigate chemical and electrochemical degradation
- Novel buffer layer strategies incorporating lithium phosphorous oxynitride (LiPON) to stabilize the electrode-electrolyte interface
Manufacturing Process Innovations:
- Cold sintering processes enabling lower temperature fabrication while maintaining high density
- Advanced dry-film manufacturing techniques reducing moisture sensitivity during production
- Scale-up strategies for sulfide-based systems using solvent-free processing
Performance Milestones:
- Demonstration of cycle life exceeding 1000 cycles with capacity retention above 80%
- Achievement of areal capacities >5 mAh/cm² with thin electrolyte layers (<50 μm)
- Operation across wider temperature ranges (-20°C to 80°C) compared to liquid electrolytes
As we stand at the threshold of this battery revolution, the question is no longer if solid-state batteries will transform the energy landscape, but when. Those who solve the core technical challenges while building scalable manufacturing processes will not just disrupt the energy storage market – they'll reshape the future of electric mobility.